Portable small meter mix machine with Stainless steel day tanks.
Hand held mixing head for small shots.
Mixing blades for day tanks.
Custom molding equipment.
Custom Molded Parts
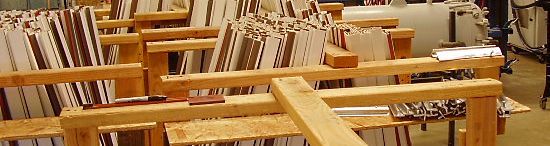
We mold custom 3D shapes and large size parts from polyurethane material using the RIM (Reaction Injection Molding). This process uses low temperatures and lower pressures then standard TIM (Thermoplastics Injection Molded) process, so tooling can be manufactured for a lower cost with shorter lead times.
The Process
Processing polyurethane is different than standard injection molding. We start off with two liquids, an Isosynate and Polyol that is meter mixed to a dipensing head, where the two materials are mixed and injected into the tool. No high temperatures to melt pellets or high tooling pressures are required. Once a mold is filled with the proper amount of material, the process is an exothermic reaction where the materials cross link and form the polyurethane part. After the curing period, the parts are demolded from the tooling and the process is repeated.
Equipment
The processing equipment for RIM is built from two basic machines, first being the meter mix equipment. This equipment is responsible for maintaining the two materials, keeping them at correct temperatures and blended at all times. The mix pumps dispense the correct flows of each material and deliver them to the mixing head where the two materials are blended prior to entering the mold cavity. The machine has a closed loop to keep materials flowing from the head and back to the day tanks during idle times to keep all materials mixed and at temperatures for the next shot. The mixing head is a very important precision piece of equipment. It can use one of three basic methods for mixing the materials. First is impingement mixing, where the two streams are sprayed at each other at high pressure, then flow out of the head at lower pressure to fill the mold. The next method of mixing is a dynamic head. A spinning meter (blade) blends the two materials prior to entering the mold. The last method is a static mixing tube. This method is used in low pressure casting where any air voids are an issue.